The in-situ facing process is crucial for achieving the desired surface finish on flanges and pedestals. Depending on the component’s size and surface finish requirements, the process can be performed using either milling or a single-point cutting tool.
Milling vs. Single-Point Cutting Tool: Which is Best for Your Needs?
- Milling:
Milling utilizes a multi-point cutting tool to machine large surfaces quickly, making it ideal for applications requiring significant material removal, such as bearing seating faces. While milling produces smooth finishes through circular strokes, it cannot meet the precision required for ASME B16.5 standard flange finishes, which are essential for creating leak-proof seals. - Single-Point Cutting Tool:
To comply with ASME B16.5 standards for gasket flanges, a single-point cutting tool or surface turning process must be used. This method ensures the grooves and serrations necessary for a secure, leak-proof seal.
Key Benefits of Our In-Situ Facing Services
- Precision Surface Finishing:
We provide accurate surface finishing for both large and small flanges, meeting stringent industry standards. - Fast Material Removal:
Our milling services allow for efficient material removal on large surfaces, saving time without compromising quality. - ASME B16.5 Compliance:
We ensure compliance with ASME B16.5 standards, delivering high-quality finishes for gasket sealing using single-point cutting methods. - Cost-Effective Solutions:
Our in-situ services reduce downtime and offer a cost-effective solution, ensuring your equipment operates efficiently and with extended longevity.
We are fully equipped with a complete range of portable pipe cutting and bevelling machines, including models from Mirage (Enerpac), DWT (Germany), and H&S (Climax). These machines are engineered to handle various pipe materials such as steel, stainless steel, super duplex, and Inconel, and are suitable for a wide range of pipe diameters, up to 36″.
Key Features of Our Portable Pipe Cutting Machines:
- Mobility:
Lightweight and easy to transport, our machines are ideal for use in confined or remote locations, minimizing downtime. - Precision Cutting:
Equipped with adjustable cutting tools or blades, they deliver accurate, burr-free cuts, whether straight or beveled. - Versatility:
Capable of performing straight, angle, and bevel cuts, these machines are suitable for a variety of applications. - User-Friendly Operation:
With automatic or semi-automatic functions, our machines reduce manual labor and ensure ease of use. - Durability:
Built for industrial use, our machines are designed to withstand harsh environments, ensuring reliable performance in heavy-duty operations.
Trust our in-situ facing services for high-performance finishes that meet industry standards. Our solutions help extend the life of your equipment while minimizing operational downtime.
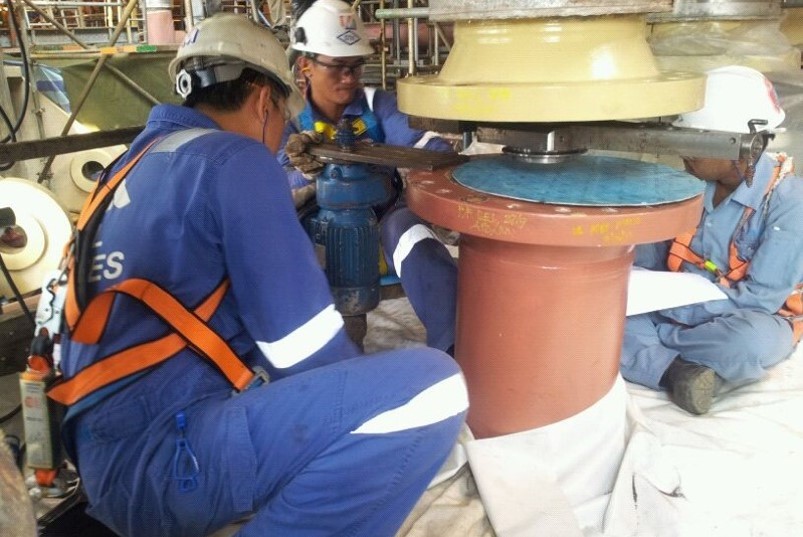
Customized low profile facer to cater for low raised flanges
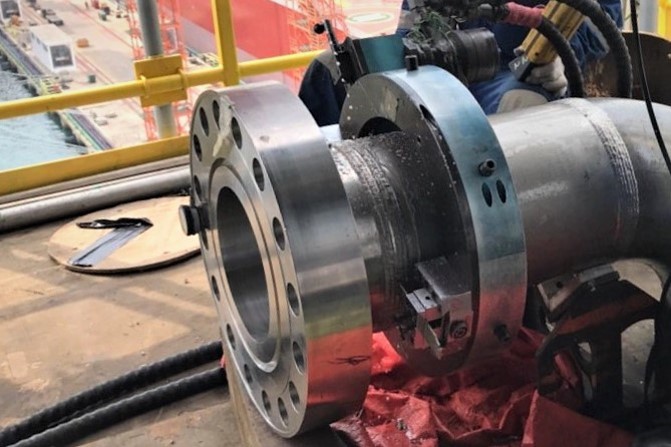
Pipe cutting on super duplex material

Pipe preparation for weld joint
Conduct valve flange facing using Climax FF1000
Pipe cutting using H&S Split Frame Clamshells AFC-28